Reference | POL 001 |
Version | 1.1 |
Issue Date | 08/05/2025 |
Approved | MD |
United Civils Limited
Health and Safety Policy
1: Introduction
1.1 Policy Overview
This Health and Safety Policy establishes the strategic framework through which United Civils Limited ensures the health, safety, and welfare of all employees, contractors, subcontractors, and any person affected by its construction activities. The policy embodies United Civils Limited’s compliance with legal duties as set out under the Health and Safety at Work etc. Act 1974, the Construction (Design and Management) Regulations 2015 (CDM 2015), other relevant legislation and ISO 45001:2018 standards.
1.2 Statement of Intent
The Managing Director of United Civils Limited fully endorses this policy and takes ultimate responsibility for ensuring its effective implementation. This policy will be displayed prominently, reviewed annually, and updated following legislative changes or significant incidents.
1.3 Legal and Regulatory Framework
This policy aligns with, and ensures compliance with, the following core legislation and standards:
-
Health and Safety at Work etc. Act 1974
-
Management of Health and Safety at Work Regulations 1999
-
CDM Regulations 2015
-
RIDDOR 2013 (Reporting of Injuries, Diseases and Dangerous Occurrences Regulations)
-
PPE Regulations 2022
-
ISO 45001:2018 Occupational Health and Safety Management System
-
The Workplace (Health, Safety and Welfare) Regulations 1992
-
Control of Substances Hazardous to Health (COSHH) 2002
2: Scope
2.1 Applicability
This policy is applicable to all employees, agency staff, contractors, subcontractors, and visitors across all operational sites and offices controlled by United Civils Limited.
3: Policy Objectives and Principles
3.1 Commitment to Safe Practice
United Civils Limited is committed to:
-
Preventing injury and ill-health.
-
Providing safe plant, equipment, and systems of work.
-
Consulting and involving workers in decisions that affect their health and safety.
-
Setting and reviewing measurable health and safety objectives.
3.2 Access to Competent Advice
A qualified Health and Safety Consultant from Sanders Environmental H&S Services Limited (SEHSS) has been appointed to advise on health and safety matters. Additionally, external consultants are retained to provide specialist construction safety guidance as required.
4: Responsibilities
4.1 Senior Management
-
Ensure sufficient resources and support for health and safety.
-
Approve all safety-related plans.
-
Sign and review the Health and Safety Policy annually.
4.2 Health and Safety Consultant
-
Develop and implement the Health and Safety Management System.
-
Conduct audits, inspections, and investigations.
-
Coordinate employee health surveillance and wellbeing strategies.
4.3 Site Managers and Supervisors
-
Ensure site-specific risk assessments and RAMS are completed before work begins.
-
Conduct daily briefings and toolbox talks.
-
Monitor subcontractor compliance.
4.4 Employees and Subcontractors
-
Follow safe systems of work and wear PPE correctly.
-
Report near misses, unsafe acts, or hazards immediately.
-
Attend mandatory health and safety training sessions.
5: Health and Safety Arrangements
5.1 Risk Assessment and Safe Systems of Work
-
Formal risk assessments and method statements (RAMS) are conducted for all activities.
-
Site-Specific Construction Phase Plans are developed in compliance with CDM 2015 (where applicable).
5.2 Drug and Alcohol Policy
-
A zero-tolerance policy is enforced.
-
Random testing may be conducted for safety-critical roles by the client.
-
Employees are educated on the client requirement and support services.
5.3 Mental Health and Wellbeing
-
Mental Health First Aiders are trained and appointed by SEHSS Limited.
-
Confidential employee assistance programmes (EAP) are available through SEHSS Limited.
-
Wellbeing initiatives such as regular breaks, fatigue management, and mental health awareness are actively promoted.
5.4 Fatigue Management
-
Working hours are managed in line with HSE and Working Time Regulations.
-
Rota systems ensure adequate rest between shifts.
5.5 Welfare Facilities
-
All sites have adequate toilets, wash stations, rest rooms, drinking water, and storage, as required by the Workplace Regulations and CDM Schedule 2.
-
Welfare facilities are established before work begins on-site.
5.6 Coordination with Other Contractors
-
Pre-start coordination meetings are conducted.
-
Shared site interface plans are established.
-
Responsibilities and procedures are clarified via written agreements and joint reviews.
6: Training, Competence and Qualifications
6.1 Induction and Mandatory Training
-
All staff receive a site-specific induction before work begins.
-
Mandatory training includes Manual Handling, Asbestos Awareness, First Aid, Slips, Trips & Falls, and COSHH Awareness.
6.2 Continuing Professional Development (CPD)
-
Regular refresher training and CPD is required for key roles.
-
Certificates and qualifications are verified and logged on a competency assessment.
6.3 Subcontractor Competency
-
Safety records and training credentials are reviewed.
-
Audits and spot-checks are conducted on active subcontractors.
7: Monitoring, Audit and Review
7.1 Safety Inspections
-
Weekly safety inspections are conducted by supervisors.
-
Monthly audits are completed by the Site Managers.
7.2 KPI Monitoring
-
Incident frequency rates, training compliance, audit non-conformances, and near-miss trends are tracked by SEHSS Limited.
7.3 Management Reviews
-
Senior management convenes with SEHSS Limited quarterly to review safety performance and compliance.
8: Incident Reporting and Enforcement
8.1 Reporting Procedures
-
All incidents must be reported immediately to a supervisor, line manager and SEHSS Limited.
-
Investigations are conducted by SEHSS Limited using root cause analysis.
8.2 RIDDOR Compliance
-
Reportable incidents are logged by SEHSS Limited and submitted to the HSE as per RIDDOR 2013 requirements.
8.3 Enforcement Action Protocol
-
All enforcement notices and improvement actions are logged.
-
Preventive measures are implemented and tracked to closure.
9: Workforce Engagement
9.1 Communication Tools
-
Toolbox talks, Safety Alerts, posters, briefings, digital updates, and newsletters are used to communicate safety messages.
10: Implementation Framework
10.1 Health and Safety Management System (HSMS)
-
Developed in accordance with ISO 45001:2018.
-
Includes policy documents, procedures, RAMS, templates, and records.
11: Policy Review
11.1 Frequency
-
This Policy will be reviewed annually or after:
-
Changes in legislation or guidance
-
Significant incidents or near misses
-
Structural changes within United Civils Limited
-
11.2 Amendment and Communication
-
Updates will be approved by the Board and communicated to all employees.
-
Latest versions are stored in the company document management system.
12: Conclusion
Through the implementation of this Health and Safety Policy, United Civils Limited reaffirms its unwavering commitment to establishing and maintaining the highest possible standards of health and safety within its construction operations. This policy serves as a cornerstone of our operational ethos, reflecting our dedication to safeguarding the wellbeing of every individual involved in or affected by our construction activities, in alignment with our legal obligations and moral imperatives.
Approved by Managing Director Scott Bland
Date: 08/05/2025
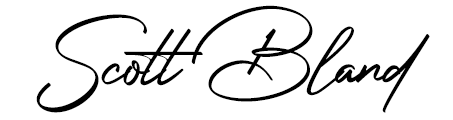